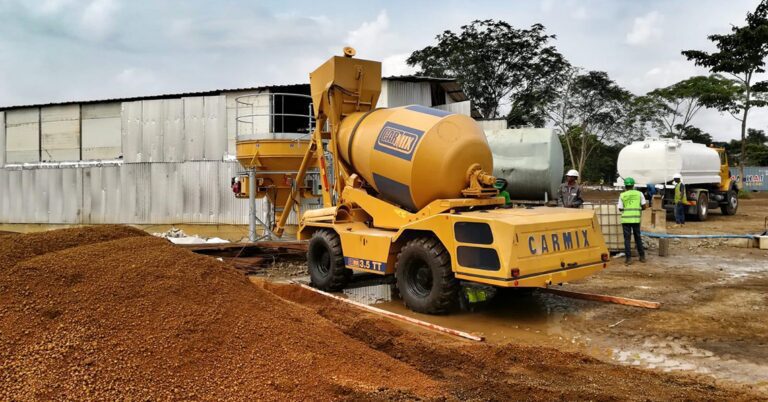
Our flagship model Carmix 3500 TC has been selected for the expansion and maintenance of the Rio Lindo hydroelectric power plant in San Francisco de Yojoa, Honduras. The Rio Lindo power plant, equally to the Cañaveral plant, uses the water of lake Yojoa and together they account for 24% of the country’s hydroelectric power generating capacity. For this important project, which started in February 2018, HCC (Hidráulica Construcción y Conservación), a world leader in design and repair of hydraulic and industrial plants, relied on the versatility and technologic performance of Carmix 3500 TC to produce large volumes of fresh concrete rapidly.
«This is the first time we use Carmix 3500TC – commented David Zepeda, General Manager at HCC – and we are very satisfied with our choice, as we can produce more than 80 m3 of concrete per day. Another big advantage is that we can see mix design data in real time and get a dosage report with the Promix and Concrete-Mate technology. All this lets us save time and above all cut the costs».
Carmix 3500 TC è una vera centrale mobile di calcestruzzo dal design “intelligente”, studiato soprattutto per offrire maggior confort all’utilizzatore con comani più ergonomici, visbilità panoramica e cabina climatizzata. Questa macchina, inoltre, è dotata di tecnologie innovative che migliorano le prestazioni del calcestruzzo: con la sonda Promix e il nuovo sistema di dosaggio Concrete-Mate è possibile, infatti, ottenere un impasto perfetto e adatto a ogni tipo di lavoro e situazione.
Promix is a measuring instrument consisting of a stainless steel probe, housed inside the mixing unit and powered by a solar panel, and of a cabin display receiving information in real time. The sensor provides data on slump, temperature, humidity, mixer rotation speed and a warning when the mix is ready. All the data is updated every ten seconds and sent to the receiver. An easy-to-read display informs the operator on the parameters of the concrete that is being prepared. This information can be stored in an external computer or sent to other mobile devices via the GPS network.
Concrete-Mate is the innovative mix design manager including an RMC Plant standard level management software which, using four sensors in the mixing unit, guarantees a top-quality concrete mix complying with international concrete production standards (UNI 206-1 – ASTM – ACI, etc) and complete control over production costs. Up to 15 different mixes and 99 types of materials can be selected with Concrete-Mate, allowing the production of multiple combinations of materials, fitting any worksite requirement. When the software has stored a mix design, it suggests to the operator the dosage of each element, the sequence of operations and the working time for each process step, thus eliminating any chance of error. Concrete-Mate can prepare concrete on site, offering a top-quality product, ready to be used anywhere, at all latitudes, rapidly and timely.